Tras una primera introducción y análisis de los puntos generales a tener en cuenta del segundo borrador del Anexo 1, en el anterior blog, en este artículo, se van a exponer los principales cambios en materia de instalaciones, equipos y servicios que han sido establecidos en la actualización.
Instalaciones
El nuevo anexo define la clasificación de grado A como la “zona crítica” para operaciones de alto riesgo a diferencia del resto de clasificaciones que las define como “áreas limpias”. Esta clasificación se consigue mediante un flujo unidireccional de aire (la nomenclatura laminar es sustituida por unidireccional); y para que esto se cumpla, indica que la entrada de personal a la zona debe minimizarse mediante el diseño de las instalaciones, equipos, procesos y procedimientos.
El área B la define como el entorno de la zona A (siempre que no haya un aislador) y las áreas C y D como áreas para realizar etapas menos críticas, pero incluyendo por primera vez el área de pesadas.
El diseño de estas nuevas zonas A y áreas B o la renovación de las existentes, debe permitir la visualización de las actividades realizadas en el interior (mediante la construcción de ventanas o instalación de cámaras de registro continuo como herramienta de investigación posterior).
En el nuevo anexo se especifica que los diferenciales de presión críticos deben estar monitorizados continuamente y que para estos puntos debe existir un sistema de alarma en caso de registrarse valores fuera de límites, a diferencia de la versión vigente de 2009 donde indica que podrán ser registradas periódicamente.
Airlocks
Se recomienda en el anexo la separación de los airlocks utilizados para la entrada/salida de materiales, de los utilizados para el movimiento del personal. En caso de que en la estrategia de control de la contaminación o Contamination Control Strategy (CCS) indique riesgo de contaminación cruzada alto, se deberán considerar también, vestuarios separados para la entrada y salida del personal. Cuando no sea posible ninguno de los casos anteriores, se debe definir en un procedimiento el tiempo mínimo requerido entre movimientos (personal/material o entrada/salida del personal).
En cuanto a los sistemas de enclavamiento, en este borrador se detalla que el interbloqueo de puertas debe ser necesario para acceso a zonas/áreas grado A y B y el sistema de advertencia visual y/o audible se utilizará en grados inferiores. Cuando sea necesario la segregación de las zonas, deberá fijarse un tiempo de demora entre el cierre y la apertura de puertas interbloqueadas que se podrá establecer/verificar con el test de recuperación de clase.
El borrador también establece que el flujo de acceso del personal debe ser de áreas de limpieza creciente, es decir, de grado D, a C y posteriormente a B pero no habla sobre el flujo de salida dejando abierta la posibilidad de realizar saltos de clase. En este mismo punto se incluye que los lavabos no deben instalarse en vestuarios de acceso directo a salas grado B y que la etapa final de los SAS, debe tener en reposo el mismo grado de limpieza (se incluye tanto viable como no viable) como la sala a la que conduce.
En cuanto a los SAS de materiales, se aclara que deben evitarse el uso de pass through, cajones pasamateriales, sin aire activo filtrado y que sus condiciones ambientales deben estar controladas y monitorizadas. Los materiales que vayan a ser transferidos a zona A, deben ir protegidos y deben incluirse en un listado aprobado desarrollado durante la validación del proceso de transferencia.
Identifica el traslado de equipos y materiales como una de las potenciales fuentes de contaminación y define que debe estar sujeto a una limpieza y desinfección acorde con el riesgo y en línea con la CCS.
Tecnologías de barrera
El actual borrador especifica que la entrada de materiales durante el proceso de fabricación debe minimizarse utilizándose tecnologías de transferencia rápida o aisladores de transferencia. Esto implica un cambio en la actual introducción de los tapones y en algunos casos de los envases de acondicionamiento primario, los cuales suelen ser cargados manualmente al equipo durante todo el proceso según las necesidades requeridas.
También define que deben minimizarse los flujos laminares tradicionales (cortinas PVC) para sustituirse por otras soluciones, Sistemas Barrera de Acceso Restringido o Restricted Access Barrier System (RABS) o aisladores abiertos o cerrados, cuando sea posible para minimizar la intervención humana directa en las zonas críticas. Su uso debe ser considerado en la CCS y cualquier enfoque alternativo debe justificarse.
Las diferencias entre estas tecnologías de barrera propuestas se basan principalmente en que los aisladores cerrados realizan la transferencia de los materiales a través de conexiones asépticas a equipos auxiliares y los aisladores abiertos permiten la entrada y/o salida de materiales de forma continua o semicontinua a través de aberturas diseñadas con sobrepresión para impedir la entrada de contaminación exterior. Para diferenciar estos últimos de los RABS, cabe destacar que los RABS no son equipos estancos y no cumplirían los criterios de fugas de contención que son requeridos para considerarse aisladores. Adicionalmente se debe asegurar un flujo de aire unidireccional positivo desde la zona crítica hacia el entorno (excepto casos especiales de contención: productos patógenos, tóxicos o radioactivos) con estudios de flujo de aire.
La clasificación de las salas en las que se encuentren estos sistemas barrera también va a depender del tipo de sistema instalado:
- RABS, la sala debe cumplir con grado B
- aisladores abiertos puede cumplir grado C o D según el resultado de una evaluación de riesgos
- aisladores cerrados debe cumplir al menos con grado D
Todas estas decisiones deben ser documentadas en la CCS.
Las pruebas de integridad o fugas de estos sistemas y de sus guantes, deben realizarse periódicamente (al principio y final de cada lote o para tamaños de lote de una unidad, puede realizarse al comienzo y final de cada sesión de fabricación).
Los guantes de los RABS se deben esterilizar antes de su instalación y esterilizarse o descontaminarse, previo a cada campaña de fabricación. La frecuencia de reemplazo de los guantes debe definirse dentro de la CCS.
En el caso de aisladores, la descontaminación debe automatizarse e incluir un agente esporicida. Para los RABS la desinfección debe incluir la aplicación rutinaria del agente esporicida mediante un método validado. En ambos casos, el tiempo de espera antes del uso de los sistemas barrera debe validarse.
Cualificaciones
Por primera vez se incluye un listado de pruebas mínimas a realizar cuando sean relevantes para el diseño o el funcionamiento de las salas o equipos, en alineación con la ISO 14644:
- Ensayo de fugas e integridad del filtro
- Medición de flujo de aire: Volumen y velocidad
- Medición diferencia de presión
- Contaje de partículas no viables
- Dirección y visualización del flujo de aire (en todos los grados, en reposo y funcionamiento e incluyendo el movimiento del aire en los “agujeros de transferencia”, paso de áreas B a C)
- Contaminación microbiana en aire y superficie (tanto en reposo como en funcionamiento)
- Recuperación
- Medición temperatura
- Medición humedad relativa
- Fugas de contención (Aisladores)
Para la clasificación de las salas se deben medir, como ya se describía en la norma, partículas iguales o superiores a 0,5 μm y 5 μm. Pero para los grados A y B se elimina el requerimiento de medición de partículas de 5 μm, pudiéndose considerar partículas de 1 μm como se establece en la normativa ISO 14644-1 (límites de 832 partículas/m3 para salas ISO 5); lo que implica una reducción de los tiempos de muestreo (muestreos de 1 minuto) ya que se requiere únicamente 24 litros. Esto no es aplicable durante la monitorización en continuo como veremos en próximos artículos.
Tabla comparativa de límites de partículas permitidos durante la clasificación:
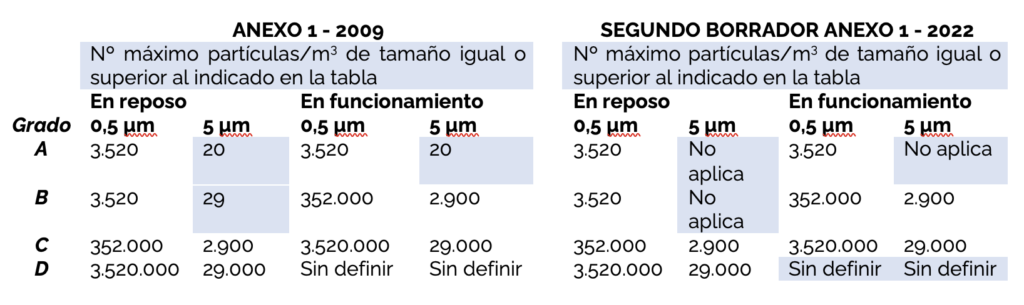
Este borrador sigue sin definir un límite de partículas para el contaje en funcionamiento en grado D, pero sí indica de forma explícita que el laboratorio debe establecerse unos límites basados en una evaluación de riesgos y datos históricos cuando corresponda.
Se mantiene el criterio de velocidad del aire de los flujos unidireccionales (valores homogéneos dentro de: 0,36 – 0,54 m/s) e indica la necesidad de realizar las mediciones a la altura de trabajo, a menos que se justifique científicamente en la CCS. No así como se describía en el primer borrador en el que se aceptaban también mediciones cerca de la cara del filtro terminal (como define la ISO 14644-3) siempre y cuando se asegurase el correcto movimiento del aire en los estudios de visualización del aire.
En el anterior anexo únicamente se hablaba de límites de contaminación microbiana durante la monitorización de las zonas o áreas limpias en funcionamiento. En este borrador se especifica que debe determinarse la concentración microbiana durante la cualificación, que debe realizarse tanto en reposo como en funcionamiento y debe verificarse mediante los 3 métodos indicados en la siguiente tabla o justificarse adecuadamente la no realización de alguno de los métodos:
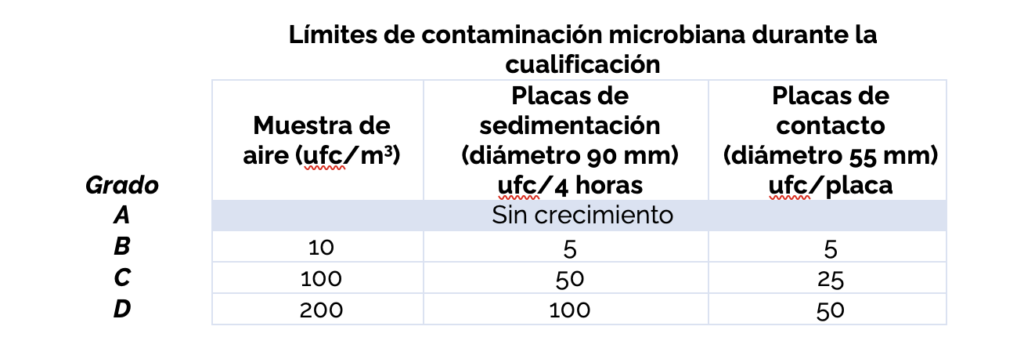
Se establecen dos cambios en cuanto a los límites, actualmente no se contempla el cálculo de medias y para grado A no debería encontrarse crecimiento, a diferencia de los controvertidos criterios anteriores: <1 (anexo 1 – 2009) o 1 (primer borrador). Así mismo, el tiempo de exposición de las placas de sedimentación debe basarse en estudios de recuperación y no debe permitir la desecación del medio.
Se detalla por primera vez la frecuencia o periodos de tiempo máximo para las recualificaciones, siendo de 6 meses para grados A y B y de 12 meses para grados C y D.
Los ensayos mínimos requeridos para las recualificaciones de salas limpias son los siguientes:
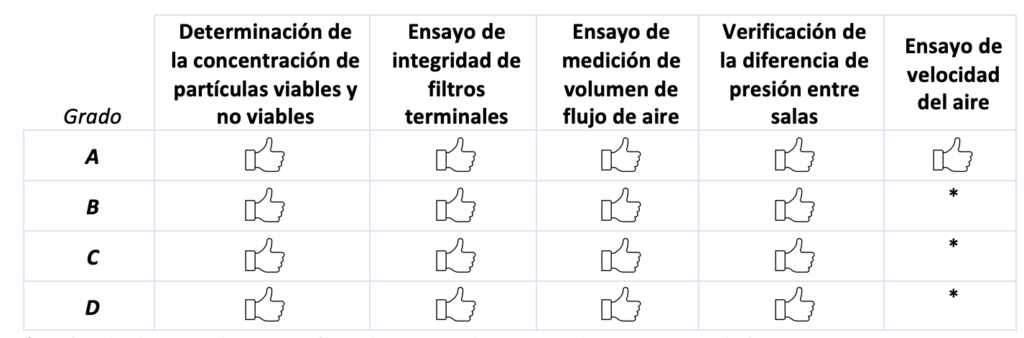
*Realizado de acuerdo a un análisis de riesgos documentado como parte de la CCS.
No incluyendo como obligatorio los ensayos de visualización del flujo de aire, ni las recuperaciones.
Así mismo, indica que se debe realizar una recualificación siempre y cuando:
- Se realice un cambio en el uso operativo de la sala o en la configuración del sistema HVAC
- Se produzca una interrupción del flujo de aire que afecte a la instalación
- Se realice un mantenimiento que afecte al funcionamiento de la instalación (sustitución de los filtros terminales)
Desinfección
En este apartado sólo se han incluido estas aclaraciones, los desinfectantes utilizados en los Grados C y D también pueden requerir esterilización, cuando estos desinfectantes sean fabricados por el fabricante se debe monitorizar la contaminación microbiana y cuando se suministren “preparados” se puede aceptar los certificados de análisis del proveedor siempre que el mismo esté homologado.
Las validaciones de limpieza deben respaldar los períodos de caducidad de las soluciones preparadas.
Equipos
El apartado de equipos se ha ampliado en este último borrador con los siguientes puntos.
Se debe disponer de una descripción detallada de los equipos y servicios (diagramas actualizados, instrumentación, listado de materiales…), verificarse en la cualificación inicial y mantenerse actualizado como parte de la revisión continua de la CCS.
Las alarmas de proceso y de los equipos deben revisarse, aprobarse y evaluarse en busca de tendencias.
Las partes en contacto indirecto (partes en contacto con componentes críticos esterilizados) también deben esterilizarse.
Los contadores de partículas, incluidos sus tubings, deben cualificarse y en el nuevo borrador se define que la longitud del tubing no debe superar 1 metro, debe tener un número mínimo de curvas y el radio de curvatura debe ser superior a 15 cm.
Servicios
En el anterior anexo no entraba mucho en detalle por lo que en el nuevo borrador se incorporan los siguientes puntos.
Los resultados de los parámetros y atributos de calidad críticos de los servicios deben estar sujetos a un análisis de tendencia regular para garantizar que las capacidades del sistema sigan siendo adecuadas.
Se debe evitar la instalación de tuberías o conductos en salas limpias siempre que sea posible.
Considera los servicios de mayor riesgo: el agua de lavado, gases y vapor utilizado en esterilización. Ampliando el último borrador que solo incluía el aire comprimido.
Sistemas de agua
Debe cualificarse los sistemas de agua con controles físico-químicos y microbiológicos teniendo en cuenta la variación estacional y cumpliendo con los requerimientos de la monografía de la Farmacopea correspondiente.
Se debe prestar especial atención al mantenimiento de los filtros instalados en el sistema y en el caso de filtros de ventilación de tanques de almacenamiento de agua para inyectables (WFI), deben esterilizarse y comprobarse la integridad de los mismos antes de su instalación y después de su uso para verificar su idoneidad.
Los planes de muestreo deben reflejar los requisitos de la CCS e incluir:
- Todos los puntos de uso, en un intervalo específico para garantizar muestras representativas para su análisis de manera regular.
- Potenciales puntos críticos de muestreo
- Una muestra del final del lazo de distribución cada día que se use el agua
Valores que excedan los niveles de alerta deben documentarse e incluir un análisis de tendencias para determinar si es un hecho aislado o si es indicativo de pérdida de control o deterioro del sistema. Se debe determinar la causa raíz y el impacto en la calidad de los productos o procesos en los que participe.
Se recomienda el uso de sensores de Carbono Orgánico Total (TOC) y conductividad on-line y su ubicación debe basarse en el riesgo y en los resultados de la cualificación.
Vapor utilizado como agente esterilizante directo
Los generadores de vapor puro deben estar diseñados, cualificados y funcionar de manera que cumplan con los niveles de sustancias químicas y endotoxinas definidos.
Cuando el vapor se utilice para esterilización directa de materiales o superficies en contacto con el producto, los condensados deben cumplir con la monografía actual para WFI de la Farmacopea. Debe existir un plan de muestreo para garantizar muestras representativas de vapor puro para su análisis regular en los que se debe analizar adicionalmente: gases no condensables, valor de sequedad y recalentamiento.
Gases y sistemas de vacío
Se incluye el cumplimiento de la calidad química, de partículas y microbiana adecuada y cuando corresponda, el cumplimiento con la monografía de la Farmacopea correspondiente.
Cuando se utilicen gases en el proceso, el control microbiano debe realizarse periódicamente.
Todas estas modificaciones pretenden cumplir el objetivo inicial que define el Anexo 1: “minimizar el riesgo de contaminación microbiológica, por partículas y pirógenos en productos estériles”. Para estar al corriente del resto de cambios no os perdáis los próximos artículos.